La impresión de objetos complejos basados en la celulosa
Los investigadores del ETH de Zúrich y de los Laboratorios Federales Suizos de Ciencia y Tecnología de Materiales (Empa) han establecido un nuevo récord mundial: imprimieron en 3D objetos complejos con un contenido de celulosa mayor que el de cualquier otra pieza de celulosa fabricada con aditivos. Para lograrlo, utilizaron un ingenioso truco.
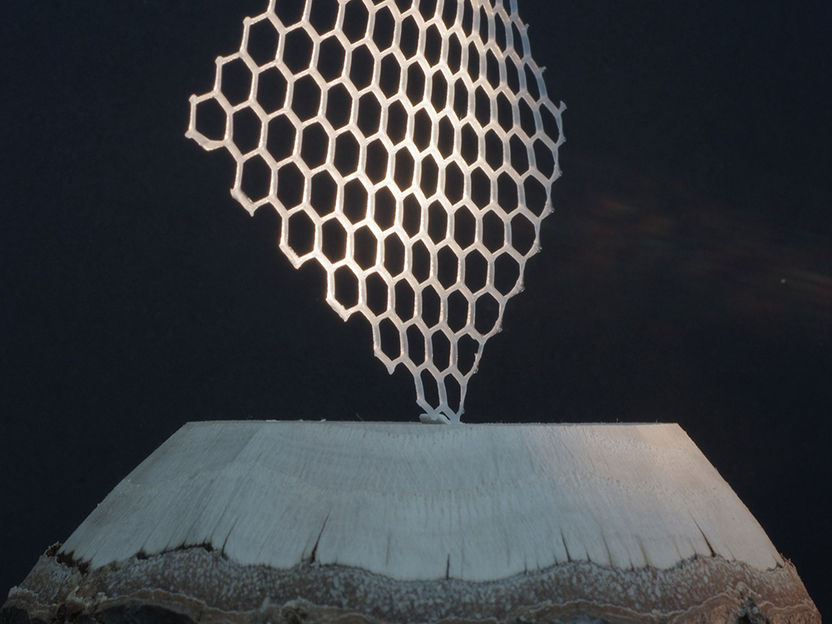
Esta estructura de panal hecha del nuevo material compuesto de celulosa es a la vez filigrana y resistente.
ETH Zürich / Empa / Michael Hausmann
Los árboles y otras plantas marcan el camino: producen la celulosa por sí mismos y la utilizan para construir estructuras complejas con extraordinarias propiedades mecánicas. Esto hace que la celulosa sea atractiva para los científicos de materiales que buscan fabricar productos sostenibles con funciones especiales. Sin embargo, el procesamiento de materiales en estructuras complejas con alto contenido de celulosa sigue siendo un gran desafío para los científicos de materiales.
Un grupo de investigadores del ETH Zurich y del Empa han encontrado ahora una manera de procesar la celulosa utilizando la impresión en 3D para crear objetos de complejidad casi ilimitada que contienen altos niveles de partículas de celulosa.
Primero se imprime, luego se densifica
Para ello, los investigadores combinaron la impresión mediante el método de escritura con tinta directa (DIW) con un proceso de densificación posterior para aumentar el contenido de celulosa del objeto impreso hasta una fracción de volumen del 27 por ciento. Su trabajo fue publicado recientemente en la revista Advanced Functional Materials.
Los investigadores del ETH y del Empa no son los primeros en procesar la celulosa con la impresora 3D. Sin embargo, los enfoques anteriores, que también utilizaban tinta que contenía celulosa, no han sido capaces de producir objetos sólidos con un contenido de celulosa tan alto y tan complejo.
La composición de la tinta de impresión es extremadamente simple. Consiste únicamente en agua en la que se han dispersado partículas de celulosa y fibras de unos pocos cientos de nanómetros. El contenido de celulosa se encuentra entre el 6 y el 14 por ciento del volumen de la tinta.
El baño de disolvente densifica la celulosa
Los investigadores del ETH utilizaron el siguiente truco para densificar los productos de celulosa impresos: Después de imprimir una tinta de agua a base de celulosa, ponen los objetos en un baño con disolventes orgánicos. Como a la celulosa no le gustan los disolventes orgánicos, las partículas tienden a agregarse. Este proceso da lugar a la contracción de la pieza impresa y, por consiguiente, a un aumento significativo de la cantidad relativa de partículas de celulosa dentro del material.
En un paso más, los científicos empaparon los objetos en una solución que contenía un precursor plástico fotosensible. Al eliminar el disolvente por evaporación, los precursores plásticos se infiltran en el andamiaje de celulosa. A continuación, para convertir los precursores plásticos en un plástico sólido, expusieron los objetos a la luz UV. Esto produjo un material compuesto con un contenido de celulosa del mencionado 27 por ciento de volumen. "El proceso de densificación nos permitió comenzar con un 6 a 14 por ciento en volumen de mezcla de agua y celulosa y terminar con un objeto compuesto que exhibe hasta un 27 por ciento en volumen de nanocristales de celulosa", dice Hausmann.
La elasticidad puede ser predeterminada
Por si esto fuera poco, dependiendo del tipo de precursor plástico utilizado, los investigadores pueden ajustar las propiedades mecánicas de los objetos impresos, como su elasticidad o resistencia. Esto les permite crear partes duras o blandas, dependiendo de la aplicación.
Utilizando este método, los investigadores pudieron fabricar varios objetos compuestos, incluyendo algunos de naturaleza delicada, como un tipo de escultura de llama de sólo 1 milímetro de espesor. Sin embargo, la densificación de las piezas impresas con un espesor de pared superior a cinco milímetros provocan una distorsión de la estructura porque la superficie del objeto que se densifica se contrae más rápido que su núcleo.
La orientación de la fibra es similar a la de la madera
Los investigadores investigaron sus objetos usando análisis de rayos X y pruebas mecánicas. Sus hallazgos mostraron que los nanocristales de celulosa están alineados de forma similar a los presentes en los materiales naturales. "Esto significa que podemos controlar la microestructura de la celulosa de nuestros objetos impresos para fabricar materiales cuya microestructura se asemeje a la de los sistemas biológicos, como la madera", dice Rafael Libanori, asistente principal en el grupo de investigación del profesor André Studart del ETH.
Las partes impresas son todavía pequeñas, a escala de laboratorio se podría decir. Pero hay muchas aplicaciones potenciales, desde embalajes personalizados hasta implantes de sustitución de cartílago para las orejas. Los investigadores también han impreso una oreja basada en un modelo humano. Sin embargo, hasta que un producto de este tipo pueda ser utilizado en la práctica clínica, se necesita más investigación y, sobre todo, ensayos clínicos.
Este tipo de tecnología de la celulosa también podría ser de interés para la industria automotriz. Los fabricantes de automóviles japoneses ya han construido un prototipo de un coche deportivo para el que las piezas de la carrocería están hechas casi en su totalidad de materiales a base de celulosa.
Nota: Este artículo ha sido traducido utilizando un sistema informático sin intervención humana. LUMITOS ofrece estas traducciones automáticas para presentar una gama más amplia de noticias de actualidad. Como este artículo ha sido traducido con traducción automática, es posible que contenga errores de vocabulario, sintaxis o gramática. El artículo original en Inglés se puede encontrar aquí.