El descubrimiento de un polímero confiere a la arena impresa en 3D una gran resistencia
Investigadores del Laboratorio Nacional de Oak Ridge del Departamento de Energía han diseñado un nuevo polímero para aglutinar y reforzar la arena de sílice para la fabricación aditiva por chorro aglutinante, un método de impresión en 3D utilizado por las industrias para la creación de prototipos y la producción de piezas.
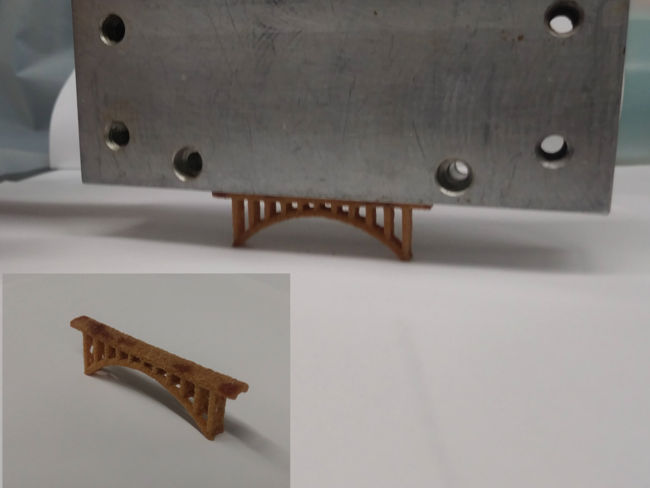
Un nuevo polímero desarrollado en el Laboratorio Nacional de Oak Ridge refuerza la arena para aplicaciones de fabricación aditiva. Un puente de arena de 6,5 centímetros impreso en 3D, que se muestra aquí, aguantó 300 veces su propio peso.
Dustin Gilmer/University of Tennessee, Knoxville
El polímero imprimible permite crear estructuras de arena con geometrías intrincadas y una resistencia excepcional, y además es soluble en agua.
El estudio, publicado en Nature Communications, muestra un puente de arena impreso en 3D que, con 6,5 centímetros, puede sostener 300 veces su propio peso, una hazaña análoga a la de 12 edificios del Empire State sentados en el puente de Brooklyn.
El proceso de impresión por chorro de tinta es más barato y rápido que otros métodos de impresión 3D utilizados por la industria y permite crear estructuras 3D a partir de diversos materiales en polvo, lo que ofrece ventajas en cuanto a costes y escalabilidad. El concepto se basa en la impresión por chorro de tinta, pero en lugar de utilizar tinta, el cabezal de la impresora lanza un polímero líquido para aglutinar un material en polvo, como la arena, construyendo un diseño 3D capa a capa. El polímero aglutinante es lo que da fuerza a la arena impresa.
El equipo utilizó sus conocimientos sobre polímeros para diseñar un aglutinante de polietileno-imina, o PEI, que duplicó la resistencia de las piezas de arena en comparación con los aglutinantes convencionales.
Las piezas impresas mediante chorro de aglutinante son inicialmente porosas cuando se retiran del lecho de impresión. Pueden reforzarse infiltrando el diseño con un material adicional de súper pegamento llamado cianoacrilato que rellena los huecos. Este segundo paso permitió multiplicar por ocho la resistencia del primer paso, lo que hace que el compuesto de polímero y arena sea más resistente que cualquier otro y cualquier material de construcción conocido, incluida la mampostería.
"Pocos polímeros son adecuados para servir de aglutinante en esta aplicación. Buscábamos propiedades específicas, como la solubilidad, que nos dieran el mejor resultado. Nuestro hallazgo clave fue la estructura molecular única de nuestro aglutinante PEI, que lo hace reactivo con el cianoacrilato para conseguir una resistencia excepcional", dijo Tomonori Saito, del ORNL, investigador principal del proyecto.
Las piezas formadas con aglutinantes convencionales se hacen más densas con materiales de infiltración, como el superpegamento, pero ninguno ha alcanzado un rendimiento cercano al del aglutinante PEI. La impresionante resistencia del aglutinante PEI se debe a la forma en que el polímero reacciona para unirse al cianoacrilato durante el curado.
Una de las posibles aplicaciones de la arena superresistente es el desarrollo de herramientas para la fabricación de materiales compuestos.
La arena de sílice es un material barato y fácil de conseguir que ha ido ganando interés en los sectores automovilístico y aeroespacial para crear piezas de materiales compuestos. Los materiales ligeros, como la fibra de carbono o la fibra de vidrio, se envuelven en núcleos de arena impresos en 3D, o "herramientas", y se curan con calor. La arena de sílice es atractiva para el utillaje porque no cambia de dimensiones cuando se calienta y porque ofrece una ventaja única en el utillaje lavable. En las aplicaciones de materiales compuestos, el uso de un aglutinante soluble en agua para formar herramientas de arena es importante porque permite un simple paso de lavado con agua del grifo para eliminar la arena, dejando una forma compuesta hueca.
"Para garantizar la precisión de las piezas de utillaje, se necesita un material que no cambie de forma durante el proceso, por lo que la arena de sílice ha sido prometedora. El reto ha sido superar la debilidad estructural de las piezas de arena", afirma Dustin Gilmer, estudiante del Centro Bredesen de la Universidad de Tennessee y autor principal del estudio.
Los actuales moldes y núcleos de fundición en arena tienen un uso industrial limitado porque los métodos comerciales, como las herramientas de lavado, aplican un calor y una presión que pueden hacer que las piezas de arena se rompan o fallen al primer intento. Se necesitan piezas de arena más resistentes para poder fabricarlas a gran escala y permitir una producción rápida de piezas.
"Nuestro compuesto de arena de polímero de alta resistencia eleva la complejidad de las piezas que se pueden fabricar con métodos de chorro de aglutinante, lo que permite geometrías más intrincadas, y amplía las aplicaciones para la fabricación, las herramientas y la construcción", dijo Gilmer.
El novedoso aglutinante ganó un premio R&D 100 2019 y ha sido licenciado por el socio industrial ExOne para la investigación.
Nota: Este artículo ha sido traducido utilizando un sistema informático sin intervención humana. LUMITOS ofrece estas traducciones automáticas para presentar una gama más amplia de noticias de actualidad. Como este artículo ha sido traducido con traducción automática, es posible que contenga errores de vocabulario, sintaxis o gramática. El artículo original en Inglés se puede encontrar aquí.