El Fraunhofer ISE demuestra la primera síntesis de metanol a largo plazo a partir de gas de alto horno en una minicentral
Optimización de procesos con el Gemelo Digital
El metanol desempeña un papel importante para la industria como producto químico básico y actualmente se considera uno de los vectores energéticos clave en la creciente economía del hidrógeno. Sin embargo, la producción convencional de metanol a partir de carbón y gas natural genera grandes cantidades de emisiones de gases de efecto invernadero. Con el proyecto Carbon2Chem®, los socios de la industria, la investigación y el mundo académico se han propuesto explorar los procesos de producción de metanol a partir de gases residuales industriales, tomando como ejemplo la industria siderúrgica.
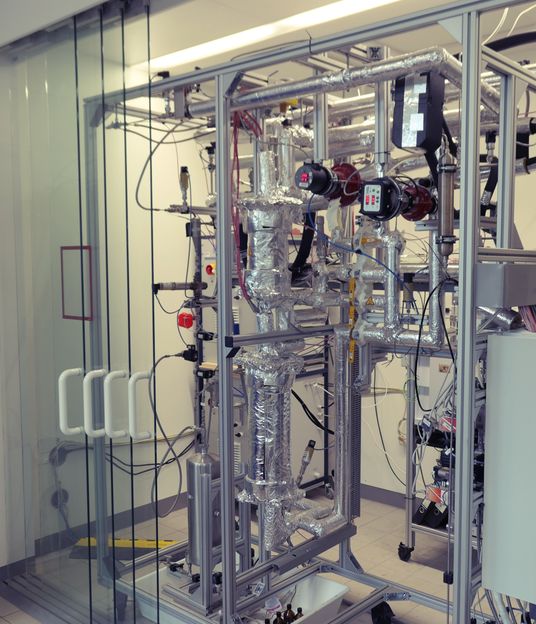
La síntesis de metanol a partir de gases metalúrgicos se demostró con éxito en la minicentral.
Fraunhofer ISE
Por primera vez, se ha demostrado la estabilidad a largo plazo de la síntesis de metanol a partir de gas de alto horno real y purificado en una minicentral del Fraunhofer ISE con una capacidad de producción de diez litros al día durante un total de más de 5.000 horas. En 2018, thyssenkrupp proporcionó la prueba de concepto para la producción de metanol a partir de gas de alto horno dentro de este proyecto.
La síntesis de metanol fósil y la producción de acero por la vía del alto horno a base de carbón son responsables de importantes emisiones de gases de efecto invernadero de CO2. Vincular ambos procesos permite sustituir el metanol procedente de combustibles puramente fósiles mediante la reacción del hidrógeno verde con las emisiones de la producción de acero. "Los compromisos del acuerdo climático de París solo pueden cumplirse vinculando los sectores industriales. Tenemos que introducir en un ciclo las emisiones que son difíciles de evitar", explica el Dr.-Ing. Achim Schaadt, jefe del Departamento de Procesos Termoquímicos del Fraunhofer ISE.
El proyecto Carbon2Chem®, que se puso en marcha en 2016 y está financiado por el Ministerio Federal de Educación e Investigación de Alemania, investiga procesos para convertir los gases de proceso de la industria del acero en productos químicos básicos. "En Carbon2Chem® se combinan las fuerzas innovadoras de la industria, la investigación aplicada y las universidades para llegar rápidamente a una solución global implementable y optimizada sistémicamente", subraya Luis F. Piedra-Garza, de thyssenkrupp Steel Europe.
Gases de escape como productos
El Fraunhofer ISE, que lleva diez años trabajando en el campo de la síntesis de metanol, se basó en un concepto de procesamiento sencillo y robusto para el desarrollo de la minicentral. Se basa en dos reactores adiabáticos no refrigerados y en un reciclaje de los gases no reaccionados al estilo industrial. La planta entró en funcionamiento a modo de prueba con gases de cilindro en el Fraunhofer ISE de Friburgo en 2017 antes de ser trasladada a la planta piloto Carbon2Chem® de Duisburgo en 2019. Los gases de escape de la acería integrada vecina se tratan en un sistema de purificación de gases de thyssenkrupp Industrial Solutions con catalizadores y sorbentes de la empresa de productos químicos especializados Clariant y están desprovistos de venenos de catalizador para la síntesis posterior. "El personal de thyssenkrupp Uhde Engineering Services mantiene el sistema de limpieza de gases en funcionamiento las 24 horas del día. La acería funciona en tres turnos, por lo que siempre hay suficiente gas. Por lo tanto, tenemos las condiciones ideales para un funcionamiento continuo a escala de planta piloto", explica Max Hadrich, jefe del grupo Power to Liquids de Fraunhofer ISE. En un total de más de 5.000 horas de funcionamiento in situ, se produjeron más de 1.500 litros de metanol crudo. El objetivo era utilizar el gas purificado de los altos hornos, que representa la mayor parte -el 85%- de los gases de las acerías. En una prueba a largo plazo que duró más de 3.000 horas, no se detectó una disminución significativa de la actividad del catalizador. Esto atestigua el buen funcionamiento del catalizador y del diseño de la planta. "Carbon2Chem® y la colaboración con Fraunhofer ISE proporcionan un marco ideal para subrayar el rendimiento de nuestros catalizadores industriales de síntesis de metanol MegaMax® para la conversión eficiente y estable de gases de proceso ricos en CO2", comenta el Dr. Andreas Geisbauer, del socio del proyecto Clariant.
Optimización del proceso con el Digital Twin
Un requisito importante para la optimización del proceso de síntesis de metanol a partir de gas de síntesis rico en CO2 es la mejora del modelo cinético para el catalizador de Clariant utilizado en Carbon2Chem®, ya que las reacciones con un bucle de reciclaje como la síntesis de metanol requieren una profunda comprensión de las complejas interacciones de los parámetros del proceso. Basándose en el modelo cinético mejorado desarrollado internamente, Fraunhofer ISE pudo crear un gemelo digital de la minicentral. Esto permite acelerar los procesos de aprendizaje y minimizar los riesgos de escalado para futuras plantas industriales: "Tras validar nuestros modelos con los datos de la minicentral, pudimos simular y optimizar los parámetros de la planta. Utilizando los resultados de la simulación, conseguimos aumentar el rendimiento de la minicentral paso a paso", informa Florian Nestler, investigador asociado del Fraunhofer ISE.
Concepto de control para la dinámica de la acería integrada
Los gases de la acería son una materia prima esencial para la planta, pero no son constantes en su cantidad y composición. Esta condición límite, que se da con frecuencia en los procesos basados en fuentes de energía renovables fluctuantes, es un nuevo reto para la síntesis de metanol. Dependiendo de las condiciones de funcionamiento o de las materias primas disponibles, las propiedades de los gases procedentes de la planta de coque, del alto horno (conversión del mineral de hierro en arrabio) o del convertidor (conversión del arrabio en acero) pueden variar considerablemente. Con los datos recogidos, ahora se puede diseñar un concepto de control que responda a los cambios en tiempo real y mantenga la síntesis en un punto de funcionamiento óptimo en todo momento.
"Estamos satisfechos de haber completado con éxito las pruebas en Duisburgo y de poder dedicarnos a la ampliación del proceso", afirma Max Hadrich. Los modelos de proceso validados se utilizarán en un siguiente paso para diseñar plantas a gran escala, realizar evaluaciones tecnoeconómicas y evaluar la huella de CO2 del proceso.
Nota: Este artículo ha sido traducido utilizando un sistema informático sin intervención humana. LUMITOS ofrece estas traducciones automáticas para presentar una gama más amplia de noticias de actualidad. Como este artículo ha sido traducido con traducción automática, es posible que contenga errores de vocabulario, sintaxis o gramática. El artículo original en Inglés se puede encontrar aquí.